Why Quality Varies Across Different Car Manufacturers
Valerie Raskovic
Jul 22, 2025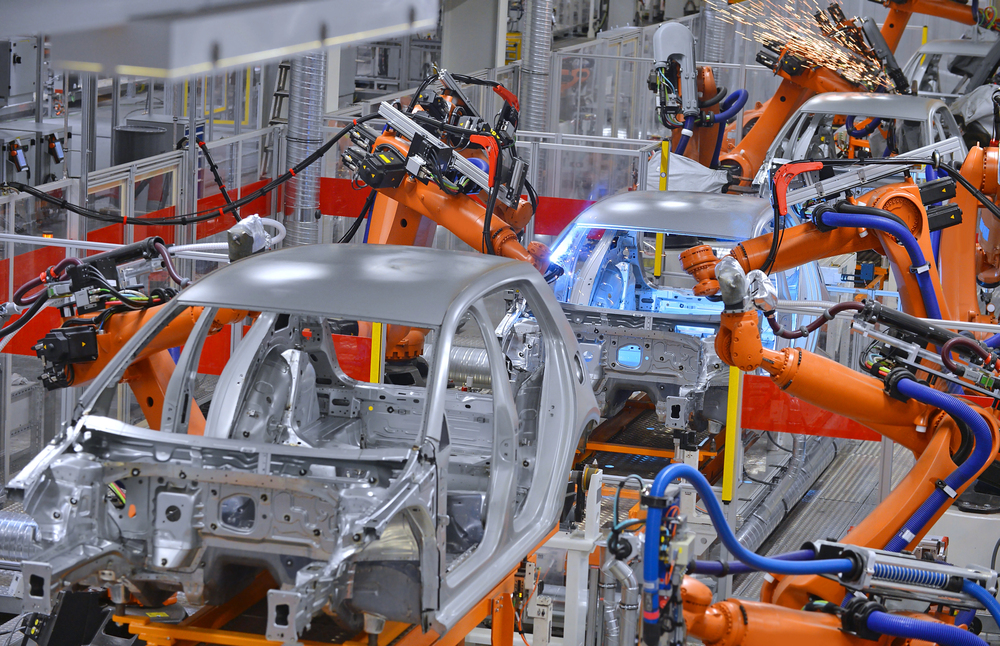
While a lot of the cars being offered for sale today may feature similar styling and design language, there are distinct differences between under the shiny new exteriors. Understanding these crucial differences can mean the difference whether you end up with a new car that depreciates rapidly and racks up costly repair bills shortly after the factory warranty expires or a car that will remain desirable and require minimal unexpected repairs.
To understand the true difference between modern cars made by various manufacturers, we must explore their individual design and manufacturing philosophies as they shape the quality, reliability and long-term value of the cars they produce.
Cost Cutting VS Reliability & Value
The length some companies go to cut costs when developing new models will vary. While all car manufacturers prioritize some cost cutting measures, some companies do it more than others. Additionally, the way cost cutting is prioritized and whether the manufacturer uses a lot of third-party parts can have a significant impact as well. While parts sharing and even platform sharing is quite common in the current car market, the way they are executed can mean the difference between success and failure. Car companies will often use parts manufactured by partners, sister companies and third-party suppliers. The amount of foreign car parts being integrated into the newly developed vehicle will vary greatly. In some cases, a manufacturer may even go so far as to completely reuse a platform developed by a sister company to rebrand the vehicle they already produced by making some cosmetic changes.
One of the most popular examples of this type of cost cutting vehicle development occurred when GM wanted to build a new compact vehicle to compete with its European rivals during the early 80’s. Instead of designing a new vehicle to break into the newly emerging compact luxury car market, GM simply took the Chevrolet Cavalier (a budget-friendly economy car) made minor cosmetic updates and rebranded it as the Cadillac Cimarron. It shared most of its parts, including the engine and chassis, with the Cavalier but carried a much higher price tag. The issue with this rebranding and the reason why the Cimarron was such a big flop for GM has to do with the fact that the Chevrolet Cavalier, which is the car it was based on, was never designed as a premium luxury car and consumers picked that up quickly. In fact, the Cimarron is often cited as one of the worst cost cutting rebranding failures in automotive history.
The Cadillac Cimarron stands as a prime example of rebranding driven by strong cost-cutting measures during vehicle development, a strategy that often extends to component sharing across multiple manufacturers. Some US Manufacturers like Mopar (Chrysler’s parts division), exemplify a cost-cutting mentality based on third-party parts cost and availability. Unlike Toyota, Mopar frequently sources parts and components from external manufacturers. While this approach helps control costs in the short term, it introduces potential vulnerabilities. Many Mopar parts are designed for specific applications but may not always be optimized for their designated use. For instance, aftermarket parts may occasionally fit unevenly or lack the thorough testing required for specific Chrysler vehicles. These parts may have compromised engineered placement within the engine or chassis, making it hard to service. This cost-focused approach can result in parts that, while cheaper upfront, offer less reliability and may lead to long-term maintenance issues. Consumer reports and warranty statistics frequently indicate higher repair claims for vehicles using many Mopar-grade components, highlighting the potential consequences of this mentality.
There are some manufacturers that put a lot of focus on innovation and advanced technology, which can also affect the vehicle’s build, quality and ease of repair. One of the most effective long-term strategies tends to be a more moderate approach of prioritizing quality engineering while adapting to new technology. This type of mentality is embraced by many Japanese brands such as Toyota and Honda.
A Consistent Trend Among Japanese Manufacturers
A significant number of Japanese manufacturers—such as Honda, Acura, Lexus, Mazda and Subaru—collectively share Toyota’s core philosophy: prioritizing engineering and long-term reliability over aggressive cost-cutting. These manufacturers similarly emphasize the use of thoroughly tested, often older technologies when proven reliable. This goes along with the idea that there is no benefit in trying to fix something that is not broken. The mentality shared amongst a lot of Japanese manufacturers reflects a belief that reliability and customer satisfaction must take priority over fruitless cost-cutting measures. Furthermore, these Japanese manufacturers exercise varying degrees of supply chain control, ensuring critical components meet their standards. This consistency across Japanese manufacturers contributes to their collective reputation for robust, long-lasting vehicles.
For example, while many car manufacturers use automatic transmissions developed by third party manufacturers like ZF Group, Toyota uses transmissions developed and manufactured by Aisin, which is part of the Toyota Group. By securing direct control over transmission production, Toyota ensures these components meet their strict engineering standards without relying on potentially inconsistent third-party suppliers. This control extends throughout their supply chain, from engines to minor components. The advantage of this approach is clear: Toyota can standardize quality, implement rigorous testing procedures and eliminate the risks associated with supplier variability. Automotive industry studies suggest vehicles with manufacturer-controlled components show a 15-20% lower rate of early failures compared to those using third party suppliers.
When examining why many Japanese cars on the market today demonstrate superior reliability compared to vehicles from some other regions, the manufacturing mentalities provide a key insight. The combination of prioritized engineering, control over supply chains and the awareness that reliability often trumps cost savings leads to vehicles requiring fewer repairs over time. Research indicates that Japanese manufacturers frequently have lower overall repair costs and more extended intervals between necessary maintenance and major repairs. For instance, comprehensive reliability studies might show Japanese vehicles require repairs only 18% as frequently as some U.S. manufacturers, highlighting the impact of manufacturing philosophy. Additionally, many Japanese vehicles may require fewer billable repair hours for the same repair than their European and domestic rivals, resulting in cars that often cost less to maintain long-term.
This exploration of manufacturer mentalities reveals how the approach to building cars—whether prioritizing immediate cost savings or long-term reliability—directly affects the quality and dependability of the final product. The contrast between Toyota’s engineered principles and manufacturers focused on cost-cutting demonstrates why some manufacturers consistently deliver more reliable vehicles, benefiting consumers seeking dependability and peace of mind.
The contrast between these approaches becomes particularly evident when examining manufacturers from different regions and their distinct philosophies toward vehicle construction.
Read more articles